Technical information
Matsuda Seisakusho’s industry-leading technology
Extensive use of CAE has helped enhance the reliability and performance of Matsuda Seisakusho products, and efficiency in design and development.
Matsuda Seisakusho has adopted an analysis tool based on the finite element method, to enhance the reliability and performance of its products, and the efficiency in design and development.
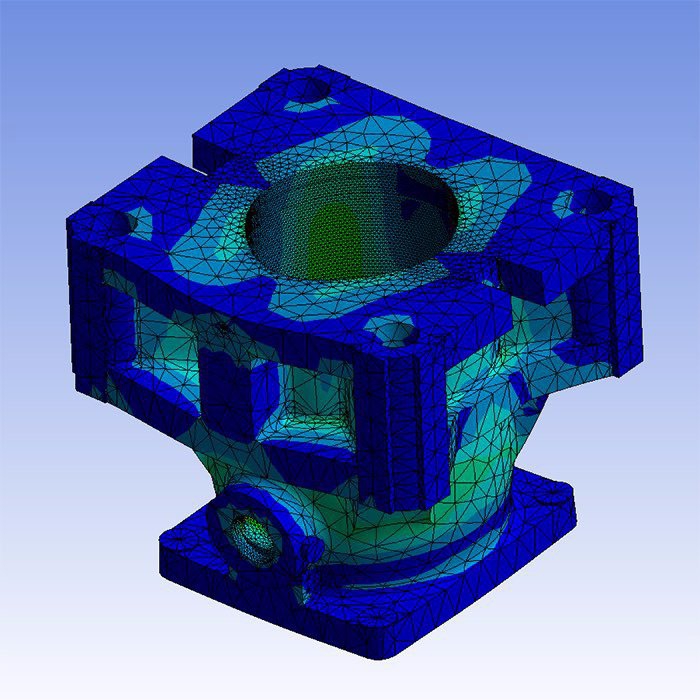
1. Enhanced reliability
It is difficult to reliably calculate the stress and deformation volume of clamping cylinders and other components of complex shapes when multiple loads and pressure are added.
Matsuda Seisakusho makes use of CAE in analysis of the stress and deformation volume, and in optimal design of shapes and material selection.
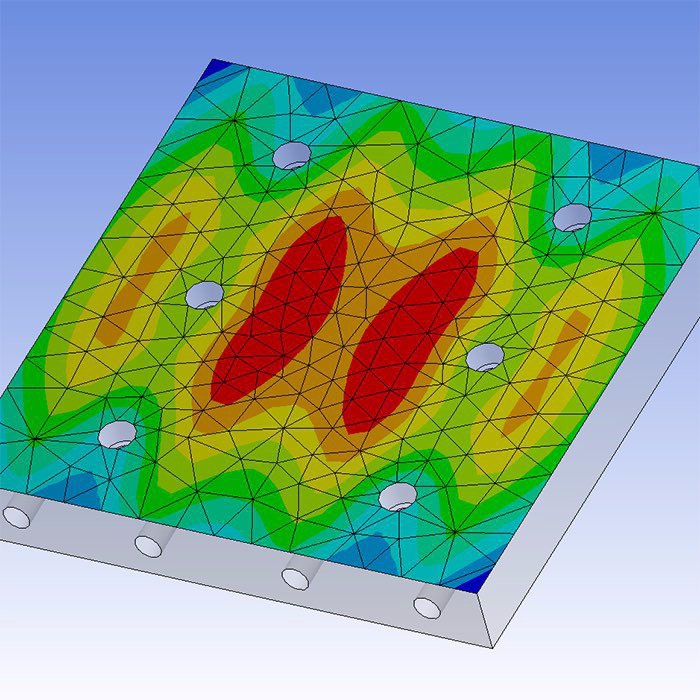
2. Enhanced performance
The heating platen that heats a mold is required to have an extreme uniformity in temperature dispersion. It is satisfied by optimizing the location of the heater on the platen and the amount of heat generation.
Matsuda conducts optimization design through CAE-based heat-transfer analysis.
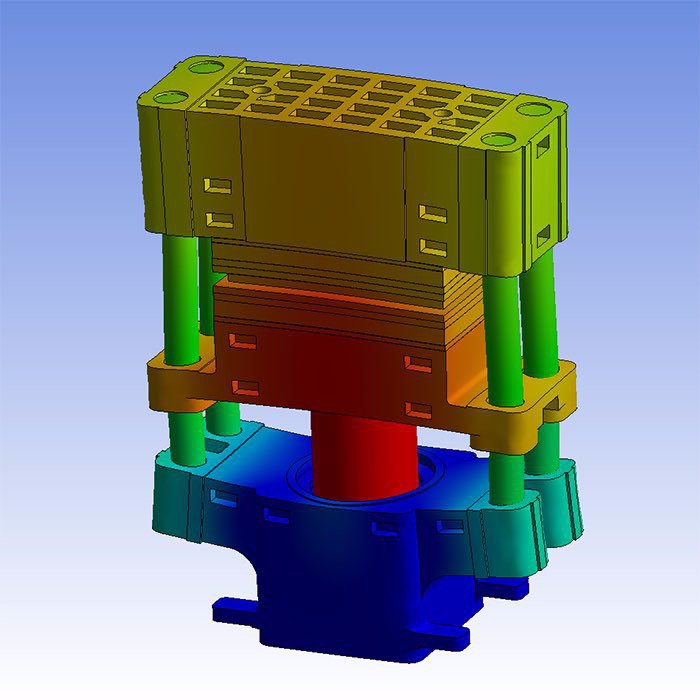
3. Enhanced efficiency in design and development
To raise efficiency in development, CAE is used for stress analysis, deformation analysis, shape optimization, and heat-transfer analysis before manufacturing of products.After analysis shows there is no problem, the prototype is evaluated and the results are checked.
Development of a second generation vent-type injection unit
Identifying the venting technology as one of the important element technologies for an injection molding machine for rubber, Matsuda Seisakusho has conducted basic testing to accumulate technical data and has improved vent technology.
The “second-generation vent-type injection unit” makes improvements over the previous vent-type units.
Matsuda’s first-generation vent-type injection units have been delivered to and used by many customers, who have then given us diverse kinds of valuable feedback and requests.
Now available to you is our second-generation vent-type injection unit, which embodies experience of our customers.
Development accomplishments
2018 | Developed a small 50-ton injection molding machine |
---|---|
2017 | Developed a new vent-type injection unit |
2017 | Developed an IoT system |
2016 | Developed a new dual-axle testing machine |
2015 | Developed the VI-V (S3) new vacuum injection molding machine for rubber |
2014 | Developed the MVE-10K vibration endurance testing machine |
2014 | Developed the VI-P (XJ) vertical-type injection molding machine for rubber |
2013 | Developed a rubber cutting machine |
2013 | Developed a dual-axle testing machine |
2011 | Developed a new vacuum injection molding machine |
2011 | Developed an internal diameter inspection equipment |
---|---|
2009 | Developed a no-burr molding method |
2009 | Developed a low-workbench injection molding machine |
2009 | Developed a 3,000-ton press machine |
2008 | Developed a vertical-type straightening machine |
2008 | Evaluated an energy-efficient pump system and adopted it in a molding machine |
2008 | Developed a vent-type injection unit |
2006 | Developed a horizontal-type 450-ton hybrid injection molding machine for BMC |
2005 | Developed a vertical-type hybrid injection molding machine for rubber |
Developed the VI-P (WJ) Series injection molding machine for rubber | |
Developed a YMDL injection molding machine |
Installation support
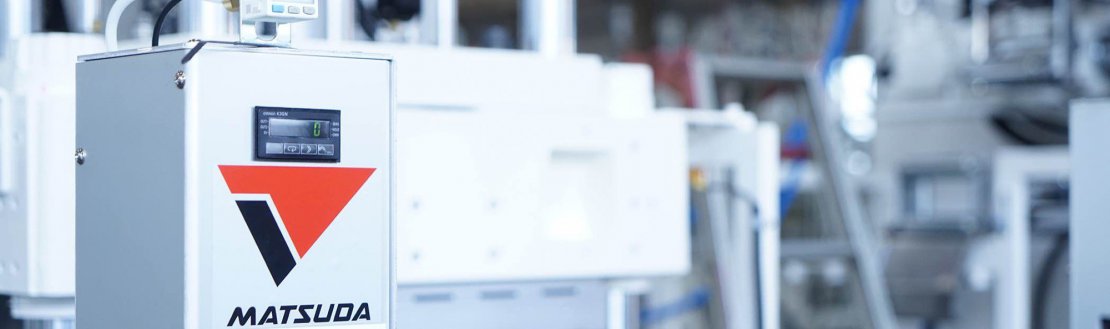
Testing by demo machines
Matsuda does molding tests for customers, using their molds and materials in our demo machines, such as the XJ Series, vacuum injection molding machines, and vent-type injection units. We are ready to do testing with your molds and materials at any time. We also have demo molds for testing. Please give us an inquiry even if you do not have your own mold.
Subsidy system
We handle documentation for various subsidies and tax incentives, such as issuance of a certificate for "Equipment for Productivity Improvement”, to be used for applying for manufacturing subsidies and taxation for the promotion of investments in small and medium-sized enterprises in Japan.
After-sales service
Our service network consists mainly of three bases in Japan and one each in Thailand and China.
We also have agencies in North and Central Americas, where we deliver prompt, advanced maintenance services to our local customers.
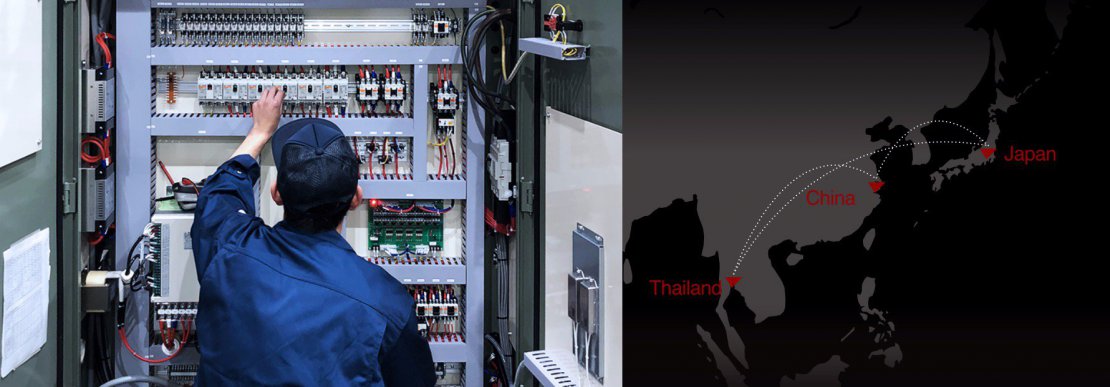
Inquiries concerning control systems
Due to suspension of production by a component maker and end of the warranty period, the old-model sequencers need to be upgraded1 to the current model if the machine becomes inoperable.Related equipment may also need to be replaced, which may take a few months, including time needed for a new design, for recovery of operability. During this period, you cannot use the molding machine. 1: There are two kinds of upgrade.
1) Replacement of the sequencer: only the sequencer is replaced while the control system remains the same.
2) Replacement of the entire control system: the entire control system is replaced by the current MAC621 (touch panel) control system.
We therefore recommend customers perform scheduled maintenance to prevent failure.
This facilitates efficient designing, compared to the case of replacing a sequencer, because the current program data can be retrieved, unlike when a request is made after the machine is entirely disabled due to a failure.
This also minimizes downtime.
However, replacement of the entire control system unit requires about one week for the work.
Models: Applicable for all models that use the MAC-501, 550 controller and ES-1000 unit.
Lead time up to the replacement
Replacement of a sequencer: 1.5-2 months after order placement
Replacement of the entire control system unit: 3-5 months after order placement
* The lead time is subject to change. Please check in advance with us.
Information on the limit in handling repair
On April 30, 2019, we stopped handling repair of the following models, mainly due to suspended production of parts and difficulty in data recovery. We ask for your understanding and cooperation.
1) Overall repair of all models of and prior to the M60
2) Replacement of a sequencer and an entire control system unit of the machines, data of which cannot be retrieved, even if they are the M61 or later models.
Please send any inquiry concerning the limit in handling repair to the Technical Service of Matsuda Seisakusho’s head office.